You want to brew craft beer but feel lost.
You worry about complex steps like mashing, lautering, and fermentation.
Follow this simple guide. It breaks down everything, from essential steps to the final pour, using clear words to ease your mind.
Overview of Craft Beer Market Data
The craft beer sector grows each year . More than 24.4 million barrels of craft beer come from the U.S. alone . Experts forecast the global craft beer market to hit $115.21 billion, with a jump to $190.7 billion by 2032, at a CAGR of about 5.9% .
Here is a table for quick reference:
Метрика | Значение | Projection (2032) | CAGR | Source |
---|---|---|---|---|
Global Craft Beer Market | $115.21 billion | $190.7 billion | 5.9% | |
U.S. Craft Beer Market | 24.4 million barrels | – | – | |
U.S. Craft Breweries | 9,552 | – | – |
Many breweries watch costs. Raw materials like malt and hops often come with a 25% price surge . Water usage can reach 4.5–8 liters per liter of beer, so wise spending on water management helps . Skilled labor also matters. Some professionals have 15+ years in big or small breweries .
Essential Craft Beer Brewing Ingredients
Most craft beer begins with four bases. These are malted grains, хмель, дрожжи, и вода . Brewers sometimes add adjuncts like fruit or oats for special flavors. Let’s keep it simple:
- Malted Grains (Barley, Wheat, Rye): Key for sugar. Malt fosters sweet extract for fermentation.
- Hops: Known for bitterness and aroma. Bittering hops go in early. Aroma hops appear later.
- Yeast (Saccharomyces cerevisiae or Saccharomyces pastorianus): Ales use warm fermentation. Lagers use cooler ranges.
- Water Chemistry: pH and mineral content shape mouthfeel.
Many prefer оборудование для малых пивоварен for test batches. Quality gear can help, whether it is a пивной бак or a пивной ферментер.
(For more insights, see our guide on оборудование для нано-пивоварни if you plan small-scale production.)
Step-by-Step Craft Beer Brewing Process
Brewers rely on a range of methods. Each step is vital to ensure quality. Let’s unpack this carefully:
Step 1: Milling
In milling, you crush grains to expose starches. The efficient crush affects brewhouse efficiency (85-90% is common). Equipment includes a зерновая мельница.
Step 2: Mashing
Next, grains mix with hot water in a сусловарочный тун. This is called затирание. Enzymes break starch into sugar. This process is saccharification. Mashing aims for the right mash temperature and pH.
Во время step mashing, you raise the temperature in stages (e.g., protein rest, saccharification rest) . Decoction uses boiling a portion of the mash to intensify malt flavor. Books highlight how small breweries can dial in mash temp to get a stable Final Gravity (FG) .
Step 3: Lautering & Sparging
Once converted, you separate the sweet сусло from grain solids . This is lautering, done in a фильтрующий чан . Промывание rinses grains to extract more sugars . The common methods are batch sparging или fly sparging .
Step 4: Wort Boiling & Hop Addition
After lautering, you boil the wort in a чайник для заваривания. Boiling takes about 60–90 minutes . The hot break forms to remove proteins. Add hops at different intervals for bitterness, flavor, and aroma . Early hops ensure bitterness. Late additions add aroma. Some breweries do whirlpooling to remove trub and hop debris .
Сухой хмель might come after the boil in the fermenter, boosting hop aroma in styles like IPAs .
Step 5: Fermentation
Next, cool wort quickly using a теплообменник или охладитель сусла . Then transfer it to a ферментер (or бродильный чан) . Подача дрожжей goes here. Temperature control matters to avoid off-flavors .
- Primary fermentation: Sugars turn to alcohol (ethanol) and CO₂ . Krausen forms on top .
- Diacetyl rest helps remove buttery tones.
During fermentation, real-time sensors can cut batch failures by 15-20% .
Step 6: Conditioning, Carbonation & Packaging
Кондиционирование smooths flavors . Some do a cold crashing to drop yeast out . A британовый бак (or яркая емкость для пива) for clarification is common.
For carbonation, choose bottle conditioning with priming sugar or force carbonation in a sealed vessel . Packaging can mean bottling, kegging, or canning . A robust packaging line might handle final steps quickly.
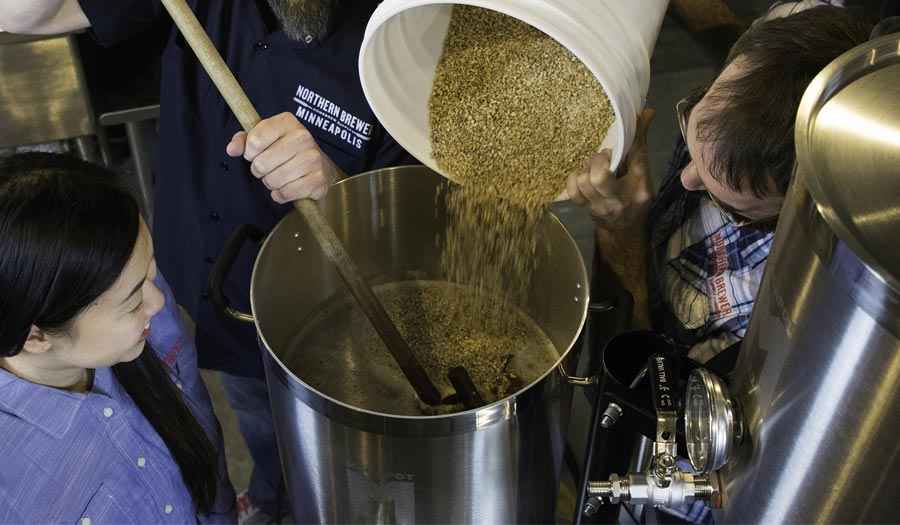
Brewing Technology & Cost
Costs vary by region. Raw materials can be 40-55% of total costs . Energy & water can be 15-25% . Labor is 20-30%. The result is that wise cost management helps small or микропивоварня setups thrive .
Table: Production Cost Breakdown
Cost Factor | % of Total Cost | Trend | Source |
---|---|---|---|
Raw Materials (Malt/Hops) | 40-55% | +25% YoY price surge | |
Energy & Water | 15-25% | 4.5–8 L water per liter of beer | |
Labor | 20-30% | Skilled brewers are key | |
Управление отходами | 5-10% | Spent grains = 85% of total waste |
Пивоварня automation can help. Tools like automated glycol systems can reduce cooling energy by 30% . Meanwhile, CO₂ recovery lowers gas costs by up to 70%.
Some advanced breweries track VDK (Vicinal Diketones) for off-flavors, which helps refine fermentation . Others use in-line carbonation to fine-tune fizz .
Quality Control & Troubleshooting
Craft beer clarity, flavor, and consistency remain top goals . One group with 15 years in R&D and production knows how to design оборудование для микропивоварен for consistent brews. They use top-level technology for controlling температура и oxygenation . Skilled professionals handle the entire design and build process without fuss.
Here is a quick table:
Проблема | Likely Cause | Решение |
---|---|---|
Неприятные запахи | Poor sanitization | Sanitize all gear well |
Облачное пиво | High protein haze | Cold crashing, filtration |
Низкое затухание | Mash temp error | Monitor mash pH, check alpha/beta amylase |
Treasure your дрожжи. Yeast strain selection can make or break a brew . Large breweries (over 1000 of them across 86 countries) have found success by focusing on robust process design. Even a simple step like trub removal can save entire batches .
Brewing Steps in More Detail
Step 1: Milling
- Process: Crush germinated, dried malt.
- Goal: Proper grain crush for high gravity yields.
- Key Terms:
- Солодовня
- Grains
- Brewhouse efficiency
- Equipment: Grain mill .
Step 2: Mashing (All-Grain Brewing vs. Extract Brewing)
- All-Grain Brewing: You mash malt from scratch.
- Экстрактное пивоварение: Use malt extracts, skipping full mashing.
- Затирание: Typically 60-90 minutes.
- Inside the Mash Tun: Time and temperature are vital. Step mashing or decoction can happen .
Step 3: Lautering & Sparging
- Лаутерный туннель: Has false bottom to separate wort .
- Batch vs. Fly Sparging: Different ways to rinse grains .
Step 4: Boil & Hop Schedule
- Boil Time: Often 60 minutes. Sometimes 90.
- Hop Schedule: Early hops for bitterness, late addition for aroma .
- Whirlpooling: Minimizes hop solids and trub.
Step 5: Fermentation
- Контроль температуры: Impacts attenuation and off-flavors .
- Yeast Management: Helps with consistency.
- Diacetyl Rest: Some do it near the end of fermentation .
Step 6: Conditioning & Packaging
- Кондиционирование: Maturing the beer.
- Cold Crashing: Clears yeast out .
- Карбонизация: Natural or forced.
- Упаковка: Kegging, bottling, or canning.
More on Brewing Technology
Fermentation kinetics matter a lot. You watch how yeast consumes sugar to turn Original Gravity (OG) to a stable Final Gravity (FG) . Some do yeast propagation in specialized tanks . Others rely on a single strain of Saccharomyces cerevisiae or use Saccharomyces pastorianus for cold fermenting lagers .
CO₂ recovery systems can catch fermentation gases, saving money. Some breweries also track Alpha acids и Beta acids in hops, ensuring consistent bitterness in the final product. The synergy of Glycol cooling helps maintain stable temperatures in fermenters .
In some corners, folks experiment with dry hopping или wet hopping to get unique aroma profiles . Hop schedule adjustments can produce a hazy look or a crisp, clear brew .
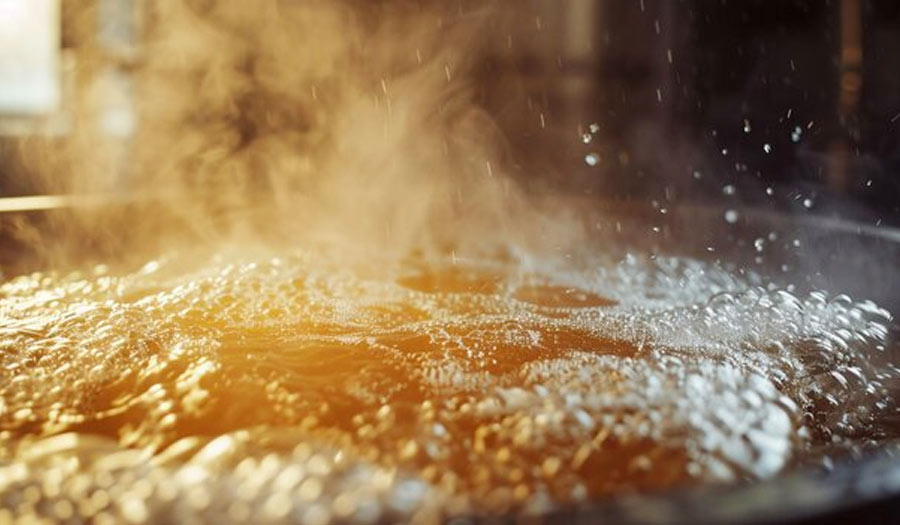
Highlighting Brewery Innovation
A certain manufacturer with over a decade of brewing equipment experience offers a 3-year warranty on tanks. They also hold a 1-year warranty on auxiliaries. That track record shows a real dedication to quality. They have 12 service centers worldwide, which means hands-on support anywhere. This can help with complicated gear like a bottle conditioning setup or a large ферментер order .
They once helped with пивоварня под ключ для продажи solutions in multiple countries. They also tailor Система для варки пива "все в одном designs, which merges сусловарочный тун, фильтрующий чан, и чайник для заваривания into one seamless operation . Skilled teams with 22 years in brewing equipment and process design stand by to help.
For brewers exploring expansions, you can see how a micro brewery system might integrate with advanced pushing lines. If you want to read more, see оборудование для мини-пивоварни for further details.
Breweries: 9,552 operations nationwide
Recent surge: 25% YoY price increase
Fermentation Monitoring: Reduces batch failures 15-20%
CO₂ Recovery: Cuts gas costs by 50-70%
Deep Dive: Beer Styles & Recipe Formulation
Стили пива abound. IPAs emphasize hop bitterness and aroma. Stouts favor dark malts with coffee notes. Recipe formulation starts with aiming for a specific Original Gravity (OG) and bitterness level in International Bitterness Units (IBU) . Some brewers track color via Standard Reference Method (SRM) for consistent hue .
Enzymes in the mash ensure protein rest for certain malt bills . Doing so can lighten the body or improve clarity. If you want a hazy IPA, you might skip certain clarifying steps .
Sensory evaluation is vital to ensure the beer meets style guidelines .
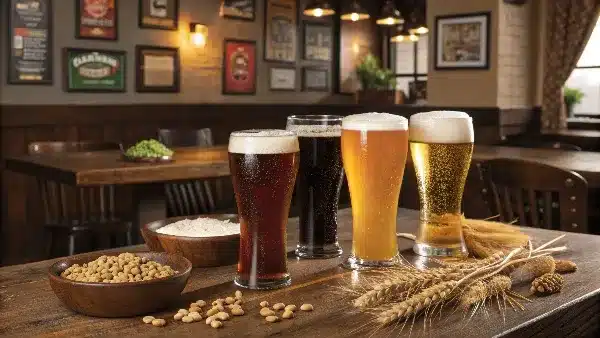
Technology Adoption and ROI
A 2024 study showed that 28% of breweries use real-time fermentation sensors . That leads to less guesswork and fewer ruined batches. About 42% adopt automated glycol systems, cutting energy costs by 30% . Only 18% have CO₂ recovery in place, but it can lower gas expenses by up to 70%.
Технология | Уровень принятия | Выгода | Case Study |
---|---|---|---|
Real-time fermentation sensors | 28% | +10% flavor consistency | Lancaster Brewery |
Automated glycol systems | 42% | -30% energy use | Escarpment Labs |
CO₂ recovery systems | 18% | Cuts gas costs by 50-70% | Micet Craft |
Many smaller setups want an Система для варки пива "все в одном to simplify operations. Part of the push is also for process optimization. This means less labor, better yield, and more consistent flavor.
Ensuring Crafting Quality
Crafting quality demands strong checks at each step . The brewer’s skill in controlling temperature, water chemistry, yeast pitching rates, and hop additions is key . Some call it a union of art and science. High-tech or not, the fundamentals remain.
Equipment alone won’t produce perfect beer. You need passion, training, and attention. For instance, a manual process might still yield world-class ales if done with care . But advanced breweries often prefer maturation vessel monitoring or in-line sensors to ensure better results .
One leading figure, a CEO with 15 years in international sales, implies that listening to brewers’ needs fosters better gear design. Their internal production chief has 13 years of building top-line fermenters. Their expert quality team with 11 years of inspection ensures each system meets advanced standards. This synergy helps them stand out for user satisfaction.
If you want compact solutions, check out nano brewery system to see how small-batch production can scale.
Beyond Beer: Distillation & Winery Growth
Brewers sometimes branch out into ликеро-водочное оборудование или оборудование для производства вина for new product lines . The same fundamentals—теплообменник, ферментер—are used, though processes differ. Many trust brands that have also ventured into distillation or winery solutions because they want a single source for all advanced gear.
Adding Value Through Brewery Design
Engineers with 22 years of brewing equipment and process design experience can tailor solutions. They consider layout, flow, and expansions. People trust them because they do not push a typical one-size-fits-all approach. Instead, they make sure they meet unique brewing needs. This approach equates to less stress and fewer hidden costs.
We see bigger interest in small batch production. People want custom recipes or seasonal brews. A flexible micro brewery setup helps them pivot quickly . They can optimize steps like whirlpooling, wort cooling, or even dry hopping for new hop varieties.
(For deeper insights, check out micro brewery setup to see how modular systems can fit your space.)
Sustainability Considerations
Studies say 75% of breweries don’t track carbon usage well . Water consumption also matters. Best practice is about 3 liters of water per liter of beer . Some breweries aim to handle spent grains (85% of total waste) by recycling or partnering with farms .
CO₂ recovery plant investments slash greenhouse gas footprints, letting breweries reuse carbon dioxide instead of venting it . Innovations like in-line carbonation free up tank space. Meanwhile, advanced gear can manage контроль температуры and limit energy use.
Closing Thoughts
Craft beer depends on tradition and technology. It merges milling, затирание, lautering, sparging, wort boiling, и ферментация into a dynamic chain. Each part, done well, yields a high-quality brew. Data shows how costs shift, how advanced sensors can reduce batch loss, and how real-time monitoring cuts failures .
A final tip is to keep learning. Some breweries refine their approach daily. They track Boil time, watch for hot break, measure cold break, and check VDK levels . They also test new hop schedules or explore adjuncts for creative beers. Search for a top-tier partner who invests in R&D. Trust a brand that has grown for 15 years, anchored by a CEO with global sales expertise and a strong design team ready to help.
If you are ready to go beyond, visit оборудование для варки пива for more info on advanced brewing systems.
Brewing is a journey. Each step is an art. Every detail, from mold-free grains to temperature precision, makes a difference. Invest time, gather data, and let your creativity thrive. You will discover that the craft beer brewing process can be both simple and endlessly rewarding.