As one of the most popular alcoholic beverages in the world, beer has undergone centuries of evolution and technological innovation, eventually developing into a highly automated and standardized production system. While distillation is not a core step in traditional beer brewing—since beer is primarily produced through fermentation rather than distillation—the application of distillation equipment has become increasingly prevalent in modern breweries. This is especially true in processes such as by-product extraction, alcohol recovery, wastewater treatment, and the production of certain specialty beers. Distillation has thus emerged as an indispensable component within advanced brewing operations. This article provides a comprehensive overview of the destilační zařízení used in breweries, discussing their types, principles, functions, and specific applications in the brewing process, with the aim of offering a thorough technical reference for industry professionals.
The Role of Distillation Technology in Breweries
Although distillation is traditionally associated with the production of spirits such as baijiu, whiskey, and vodka, its role in modern breweries is gradually becoming more prominent. This technology plays a significant part in several key areas:
- Alcohol Recovery and Reuse: During fermentation or packaging, alcohol vapor is often generated and lost to the environment. By utilizing condensation and distillation equipment, breweries can effectively recover this alcohol, improving resource utilization and sustainability.
- By-Product Extraction: Distillation equipment is also used to extract valuable compounds such as hop oils and yeast-derived by-products. These can serve as raw materials for flavorings, food additives, and other commercial applications.
- Wastewater Treatment: Brewery wastewater may contain residual alcohol or other volatile organic compounds (VOCs). Distillation technology allows for their effective separation and purification, contributing to environmental compliance and cleaner discharge.
- Production of Specialty Beers: For instance, vacuum distillation is commonly employed in the production of non-alcoholic or low-alcohol beers. This method removes alcohol at lower temperatures, helping preserve the original flavor profile of the beer.
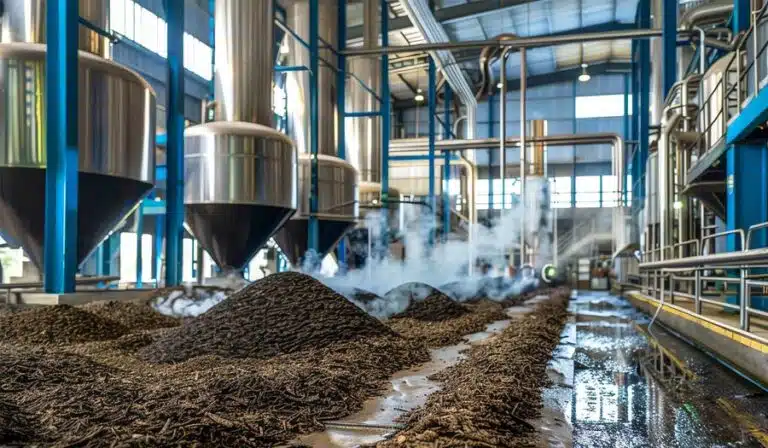
Common Types of Distillation Equipment Used in Breweries
Hrnce v klidu
- Structural Features: Primarily consists of a heating pot (boiler), a swan neck or column, and a condenser. It is simple in design and operation.
- Application Scenarios: Suitable for small-scale operations and by-product extraction, such as hop essential oils or experimental flavor components.
- Advantages: Excellent flavor retention, low equipment cost, and ideal for craft or artisanal brewing environments.
- Disadvantages: Low efficiency, relatively high energy consumption, and unsuitable for continuous production.
Continuous Distillation Column
- Structural Composition: Includes a reboiler, rectification column, condenser, and reflux control system.
- Application Scenarios: Commonly used in large-scale operations for alcohol recovery or the production of non-alcoholic beer.
- Advantages: High efficiency, consistent product purity, and compatibility with automation.
- Disadvantages: Complex structure and higher initial capital investment.
Vacuum Distillation Unit
- Principle: Operates under sub-atmospheric pressure to lower boiling points, thereby reducing thermal degradation of flavor compounds.
- Application Scenarios: Ideal for producing alcohol-free beers and low-temperature purification in premium craft beer production.
- Advantages: Superior flavor preservation and suitable for thermally sensitive ingredients.
- Disadvantages: Requires precise pressure control systems and entails higher operational complexity.
Membrane Distillation
- Structural Principle: Combines thermal and membrane separation techniques, where vapor passes through a hydrophobic membrane driven by a temperature gradient.
- Application Scenarios: An emerging technology being tested in fields such as high-efficiency alcohol removal and water reuse.
- Advantages: Energy-efficient, easily integrated with automated systems.
- Disadvantages: High cost and membrane fouling remain challenges to be addressed.

Key Structural Components of Distillation Equipment
Distillation Column
- Material: Carbon steel, stainless steel, or special alloy steels.
- Structure: A vertical cylindrical vessel composed of a column body, bottom pot (kettle), flanges, manholes, and column sections.
- Function: Provides space for vapor–liquid contact and phase separation.
Trays or Packing Layers
- Tray Types: Bubble-cap trays, sieve trays, valve trays.
- Packing Types: Random packings (e.g., Raschig rings, Pall rings) and structured packings (e.g., metal corrugated sheets).
- Function: Enhance vapor–liquid interaction and improve mass transfer efficiency.
Reboiler
- Structure Types: Shell-and-tube (typical), thermosiphon reboiler, and forced circulation reboiler.
- Function: Supplies heat to the liquid at the bottom of the column, partially vaporizing it to produce upward-flowing vapor, enabling continuous distillation.
Kondenzátor
- Total Condenser: Fully condenses all overhead vapor into liquid.
- Partial Condenser: Partially condenses vapor, allowing adjustment of the reflux ratio.
- Structure: Typically shell-and-tube design, with separate paths for cooling water and process vapor.
- Function: The condensed liquid is directed to either the reflux drum or product collection tank.
Reflux Drum
- Function: Stores condensed overhead liquid and splits it between reflux and overhead product.
- Components: Equipped with reflux pumps and control valves.
- Role: Maintains the reflux ratio (ratio of reflux to distillate) and stabilizes top column composition.
Bottom Kettle (Column Base Reservoir)
- Structure: The bottom section of the column serving as a liquid collection vessel; often integrated with a heating system or connected to the reboiler.
- Function: Collects heavy components (bottoms product) and supplies liquid to the reboiler for recirculation.
Feed System
- Feed Inlet: Located at different heights of the column depending on feed characteristics and separation goals.
- Distributors or Feed Pipes: Ensure even distribution of feed across the column cross-section to avoid maldistribution or local flooding.
Instrumentation and Automatic Control System
- Sensors: Temperature sensors (at top, middle, bottom), pressure transmitters, level gauges, and flow meters.
- Function: Ensure stable operation by controlling column temperature profiles, pressure, and reflux ratio.
- Goal: Maintain product purity, ensure process stability, and support safe system operation.
Process Flow Example of a Distillation System in Breweries
Process Application Background
Although finished beer itself does not require distillation, the distillation process plays a critical role in handling by-products and producing non-alcoholic beer. Common applications include recovering low-concentration ethanol from fermentation liquids or removing ethanol from regular beer to produce low- or non-alcoholic beverages. This not only supports resource recycling but also meets modern beverage market demands for health-conscious and environmentally friendly products.
Pretreatment of Feed Liquid
The feedstock typically consists of post-fermentation residue, low-alcohol beer, or ethanol recovery streams containing about 1–5% ethanol. Before entering the distillation system, the liquid must undergo coarse or fine filtration to remove yeast residue and other solids, preventing equipment blockage. Additionally, temperature and pH must be adjusted to ensure optimal conditions for efficient separation within the distillation column.
Separation in the Distillation Column
The pretreated liquid is heated to the ethanol boiling point (~78.5°C) and introduced into the middle section of a rectification column. The distillation column is usually of continuous type, equipped with internal trays or packing to maximize vapor–liquid contact surface. A reboiler at the bottom supplies thermal energy, causing ethanol to vaporize and rise through the column, while water and other heavier components flow downward. This enables effective separation of ethanol from the mixture, producing a continuous output of high-purity ethanol vapor.
Alcohol Recovery and Reflux Control
The top of the distillation column connects to a condenser, where rising ethanol vapors are cooled and condensed into liquid form for recovery. A portion of the condensate is returned to the column as reflux to enhance separation efficiency. An automated control system precisely regulates the reflux ratio, stabilizing the internal temperature profile of the column and ensuring the recovered ethanol meets the required concentration (e.g., above 90%).
De-alcoholized Residue Handling and System Integration
The bottom product from the column is a low- or non-alcoholic beer liquid or waste stream. Depending on process requirements, it can be directed to downstream pasteurization and packaging stages or sent to a wastewater treatment facility. The entire distillation system is typically integrated with temperature, pressure, level, and flow sensors for automated operation and energy optimization. Heat recovery designs are often included to reduce energy consumption and improve economic efficiency.
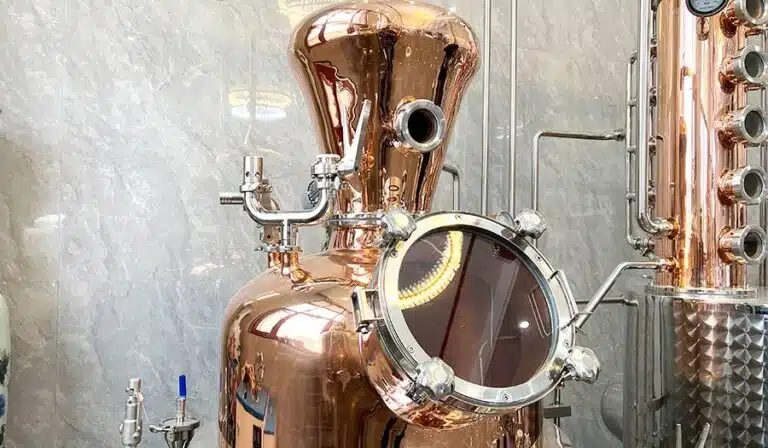
Distillation Equipment Selection Recommendations and Operation & Maintenance Key Points
Distillation Equipment Selection Recommendations
- Production Scale: Small craft breweries are suitable for batch distillation or vacuum distillation equipment; medium to large factories are better suited for continuous column systems.
- Process Purpose: If the goal is alcohol removal, vacuum distillation should be prioritized; if for by-product extraction, traditional pot stills can be considered.
- Automation Requirements: Highly automated systems should be equipped with PLC or DCS control to reduce human error.
Operation and Maintenance Key Points
- Regularly check the sealing integrity, vacuum pump performance, and the heat exchange efficiency of the condensation system.
- Pay attention to fouling inside the column and perform periodic CIP (Clean-In-Place) cleaning.
- Monitor alcohol concentration at each discharge point and maintain data records for traceability.
- Be mindful of the equipment materials’ resistance to acids and alkalis to prevent corrosion.
Contributions to Environmental Protection and Sustainability
Distillation equipment not only improves resource utilization efficiency in beer production but also contributes environmentally:
- Alcohol Volatilization Control: Reduces VOC emissions, helping to meet emission standards.
- Energy Recovery: Some distillation systems integrate heat exchange units to recover and reuse waste heat.
- Water Recycling: Water separated through distillation can be reused for onsite landscaping or cleaning.
Závěr
With the booming craft beer market and consumers’ diverse demands for healthy beverages, production processes in breweries continue to upgrade. Destilační zařízení, as an important auxiliary tool, plays an increasingly indispensable role. From by-product extraction to alcohol-free beer production, from alcohol recovery and reuse to wastewater treatment, distillation equipment—with its high efficiency, environmental friendliness, and stability—is driving the beer industry toward higher quality, greater efficiency, and greener development. Looking ahead, with the further advancement of automation control, intelligent manufacturing, and new separation technologies, distillation systems will become more refined and integrated, offering broader technological and commercial value to the beer industry.