Craft distillers and commercial spirits producers face a common problem: selecting the right distillation equipment can make or break your operation. With the global distillation systems market projected to reach $15.2 billion by 2032 (growing at a 7.9% CAGR), the choices can seem overwhelming.
When your reputation, product quality, and profit margins all depend on your equipment choices, how do you avoid costly mistakes?
Understanding Alcohol Distillation Equipment
At its most basic, distillation equipment separates alcohol from water and other components through controlled heating and cooling. But the reality is far more complex.
Many new distillers discover too late that their equipment choices limit their product range, production capacity, and even their legal compliance. With craft distilleries growing at 15% annually since 2020, competition is fierce, and equipment failures can spell disaster.
The team at Micet, with over 15 years of experience helping set up more than 1000 breweries and distilleries across 86 countries, has seen these problems firsthand. Their CEO Nancy has spent 15 years in international sales understanding exactly what challenges distillers face.
Key Components Explained: Stills, Condensers, Fermentation Tanks
Every distillation system needs these core components:
- Stills – The heart of your distillation system
- Condensers – Transform vapor back into liquid form
- Fermentation tanks – Where initial alcohol production occurs
- Boiler systems – Provide necessary heat for distillation
- Cooling systems – Maintain optimal temperatures
The quality of these components directly impacts your final product’s taste, consistency, and production efficiency.
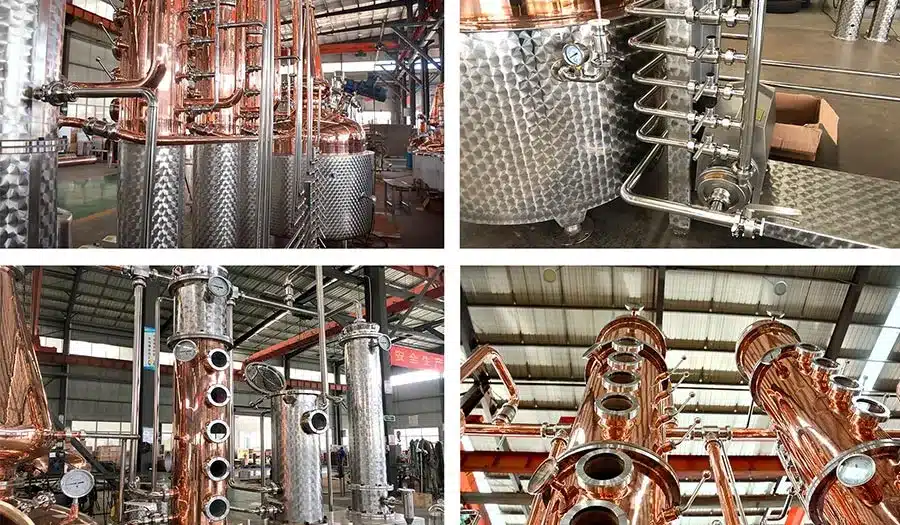
Copper vs. Stainless Steel: Impact on Flavor & Durability
Did you know that 63% of premium spirit producers use copper stills for flavor control? Here’s why material choice matters:
Material | Pros | Cons | Best For |
---|---|---|---|
Copper | Removes sulfur compounds, enhances flavor | Higher cost, requires more maintenance | Whiskey, rum, brandy |
Stainless Steel | Durable, easier to clean, lower cost | Less flavor interaction | Vodka, gin, neutral spirits |
Hybrid Systems | Combines benefits of both | Higher upfront investment | Versatile distilleries producing multiple spirits |
Micet’s production director, with 13 years of experience, has overseen the manufacturing of all three types, ensuring each meets the highest quality standards for durability and performance.
Types of Equipment
Commercial vs. Home Use Distillation Systems
The equipment needs for a home hobbyist versus a commercial distillery are vastly different, not just in scale but in design, safety features, and regulatory compliance.
Pot Stills (Tradition-Driven: Whiskey/Rum)
Pot stills remain the traditional choice for flavor-forward spirits like whiskey and rum. These stills:
- Preserve flavor compounds and congeners
- Operate in batches rather than continuously
- Often feature copper construction for chemical interaction
- Require more skill and attention during operation
Micet’s 1000L Beer Brewing System can be adapted with distillation components to create a complete brewing and distillation operation, perfect for brewpubs looking to expand into spirits.
Column Stills (Efficiency-Focused: Vodka/Gin)
For neutral spirits and high-volume production, column stills offer significant advantages:
- Higher alcohol purity (up to 95% ABV)
- Continuous operation capabilities
- More efficient energy use
- Better consistency between batches
Column stills use fractional distillation to achieve greater separation of volatile compounds, resulting in cleaner spirits.
Hybrid Systems: Flexibility for Craft Distilleries
Modern craft distilleries often choose hybrid systems that combine pot still flavor with column still efficiency. These systems:
- Allow production of multiple spirit types
- Can be reconfigured for different recipes
- Optimize space usage
- Provide growth flexibility
Micet’s engineering team has designed custom hybrid systems for distilleries across five continents, ensuring each client can produce their full product range without unnecessary equipment duplication.
Critical Features
5 Must-Have Features for Safe, Efficient Distillation
1. ASME-Certified Boilers (Legal Compliance & Safety)
Pressure vessel safety is non-negotiable. ASME certification ensures your boiler system meets rigorous safety standards, preventing potentially catastrophic failures.
Did you know? TTB-approved equipment reduces compliance failures by 40%. Micet’s quality inspectors with 11 years of expertise ensure every component meets or exceeds these standards.
2. Automated Temperature Controls (Prevent Overheating)
Modern distillation requires precision. Automated temperature control systems:
- Maintain optimal distillation temperatures
- Prevent product-ruining overheating
- Reduce operator workload
- Improve batch consistency
3. Modular Designs for Scalability
As your distillery grows, your equipment should grow with you. Modular systems allow for:
- Phased investment as your business expands
- Reconfiguration for different product lines
- Easier maintenance and part replacement
- Space-efficient layouts
Micet’s service team, with 22 years of brewing equipment and process design experience, specializes in creating scalable solutions that grow with your business.
4. Proofing Hydrometers and Testing Equipment
Precise measurement of alcohol content is essential for both quality control and regulatory compliance. Professional-grade testing equipment ensures:
- Accurate alcohol by volume (ABV) readings
- Consistent product quality
- Documentation for compliance purposes
- Process optimization
5. Proper Ventilation Systems
Alcohol vapor can create both safety and quality issues. Proper ventilation:
- Reduces explosion risks
- Improves air quality for workers
- Prevents contamination
- Meets regulatory requirements
Micet’s High-Quality Distillery Equipment integrates comprehensive safety features while maintaining production efficiency.
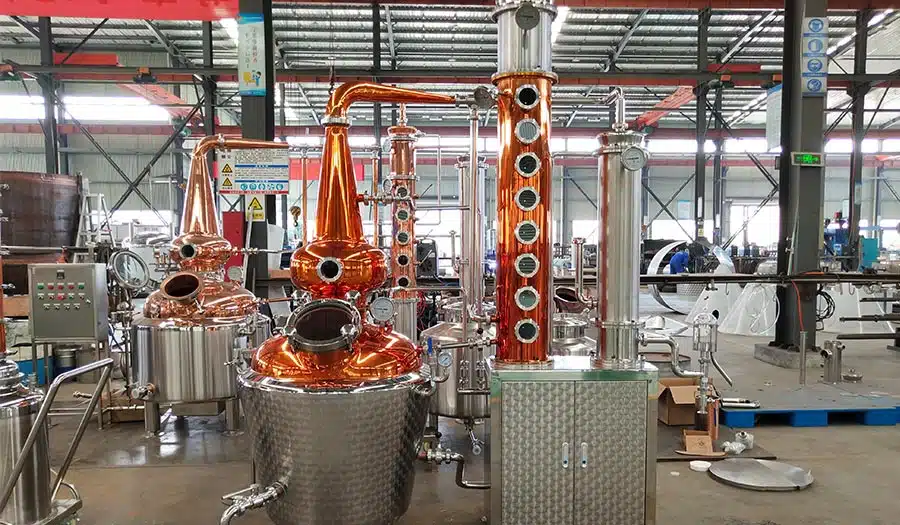
Legal Compliance
Navigating TTB Regulations & Licensing
The Alcohol and Tobacco Tax and Trade Bureau (TTB) strictly regulates distillery operations. Non-compliance can result in:
- Operation shutdowns
- Heavy fines
- Loss of permits
- Criminal charges
Micet’s team includes regulatory experts who help clients navigate these complex requirements, from equipment specifications to facility design.
FDA-Grade Materials Checklist
All spirits production equipment must use food-grade materials. A comprehensive checklist includes:
- 304 or 316 stainless steel for product contact surfaces
- Food-safe gaskets and seals
- Lead-free solder connections
- Properly finished welds
- Certified cleaning protocols
Avoiding Common Compliance Failures
The most frequent compliance issues include:
- Inadequate record-keeping systems
- Improper gauge calibration
- Insufficient security measures
- Non-compliant equipment modifications
- Inadequate product testing procedures
With 12 service centers and agent offices worldwide, Micet provides ongoing compliance support long after initial installation.
Actionable Guides
How to Choose Equipment: 7-Step Checklist
- Define your production goals – Volume, spirit types, growth plans
- Establish your budget – Including installation and auxiliary systems
- Assess your space constraints – Height, floor load, access points
- Determine your energy sources – Steam, electric, direct fire
- Plan for waste management – Cooling water, spent wash, cleaning chemicals
- Consider automation level – Manual, semi-automated, or fully automated
- Evaluate manufacturer support – Training, warranties, spare parts availability
Micet offers a 3-year warranty on tanks and a 1-year warranty on auxiliaries and accessories, demonstrating confidence in their equipment quality.
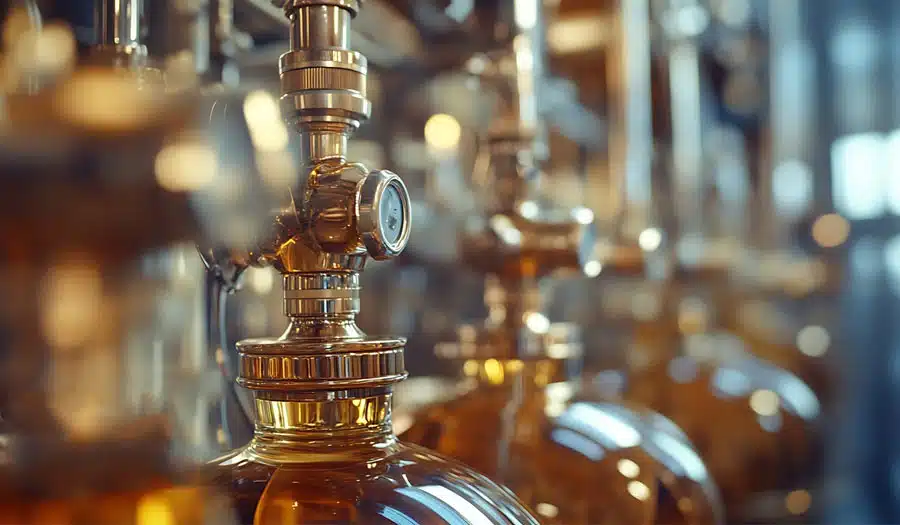
$5k vs. $50k Systems: ROI Breakdown
Investment in quality equipment pays dividends over time:
System Level | Initial Cost | Production Capacity | Expected Lifespan | Maintenance Costs | Product Quality Control |
---|---|---|---|---|---|
Entry-Level | $5,000-$15,000 | 50-200L/month | 5-7 years | Higher per unit | Basic |
Mid-Range | $15,000-$50,000 | 500-2,000L/month | 10-15 years | Moderate | Good |
Professional | $50,000+ | 2,000L+/month | 15-20+ years | Lower per unit | Excellent |
Hidden Costs (Ventilation, Energy, Maintenance)
Beyond the equipment itself, budget for:
- Ventilation systems: $5,000-$25,000
- Energy consumption: Often 20-30% of operating costs
- Regular maintenance: 5-10% of equipment value annually
- Operator training: Often overlooked but critical
- Compliance testing: Required for commercial operations
Maintenance & Safety
Daily/Weekly Maintenance Protocols
Proper maintenance extends equipment life and ensures safe operation:
Daily Tasks:
- Clean all product contact surfaces
- Check temperature and pressure gauges
- Inspect gaskets and seals
- Monitor cooling water quality
Weekly Tasks:
- Deep clean condensers
- Check electrical connections
- Test safety valves
- Calibrate measuring instruments
Cleaning Solvents Safe for Copper
Copper stills require special care to maintain their beneficial properties:
- Use food-grade citric acid solutions for scale removal
- Avoid abrasive cleaning tools
- Rinse thoroughly with distilled water
- Allow complete drying before next use
Fire Suppression System Setup
Distilleries present unique fire risks due to alcohol vapor and high heat:
- Class B fire extinguishers positioned strategically
- Automatic suppression systems for larger operations
- Emergency shutdown procedures
- Staff training for fire response
Micet’s Stainless Steel Vessel solutions include integrated safety features that exceed industry standards while maintaining operational efficiency.
Market Trends and Innovations
The alcohol distillation equipment market continues to evolve rapidly. Key trends include:
AI-Driven Automation
AI systems are revolutionizing distillation. The Next Century Spirits case study demonstrates:
- Batch time reduced from 14 days to less than 24 hours
- 22% higher product consistency
- Reduced labor requirements
- Lower energy consumption
Environmental Sustainability
Modern distillation equipment focuses on reducing environmental impact:
- Energy-efficient systems reduce CO2 emissions by 12%
- 65% of EU distilleries now use waste-recycling distillation columns
- Water recycling systems minimize consumption
- Spent mash repurposing for agricultural uses
Global Market Growth
The spirits market continues to expand rapidly, with:
- Global spirits market projected to reach $5,716.2 billion by 2032
- Craft segments growing faster than traditional markets
- Asia-Pacific region holding 48% market share
- North American growth driven by premium whiskey production
Micet stays at the forefront of these trends through continuous R&D and adaptation, helping clients implement the latest innovations.
FAQs
Can I use homemade equipment legally?
No. Commercial distillation requires federally approved equipment that meets safety and regulatory standards. Homemade equipment is illegal for commercial spirits production and dangerous due to explosion and contamination risks.
Best still for moonshine beginners?
For legal home distilling in countries where permitted, beginners should start with a small (5-10 gallon) pot still with copper components. Focus on simple designs with good temperature control and safety features.
How much does a complete distillery system cost?
Complete small commercial systems typically range from $50,000 to $500,000, depending on capacity, automation level, and features. Micet offers customized solutions starting at $75,000 for complete turnkey operations.
Are copper stills worth the extra cost?
For flavor-forward spirits like whiskey and rum, absolutely yes. Copper removes sulfur compounds and contributes beneficial flavor reactions. For neutral spirits like vodka, stainless steel may be more cost-effective.
How long does professional equipment last?
Quality distillation equipment from reputable manufacturers like Micet typically lasts 15-20+ years with proper maintenance. Many systems can be upgraded over time to extend their useful life.
Conclusion
Selecting the right alcohol distillation equipment represents one of the most critical decisions for any distillery operation. With the market growing at nearly 8% annually and competition intensifying, your equipment choices directly impact product quality, operational efficiency, and ultimately, business success.
The best approach combines thorough research, clear production goals, and partnership with experienced equipment manufacturers who understand the unique challenges of distillation. Companies like Micet, with 15 years of experience setting up over 1000 breweries and distilleries worldwide, offer not just equipment but complete solutions tailored to each client’s needs.
Whether you’re launching a craft distillery or expanding an existing operation, investing in quality equipment with proper support will pay dividends through consistent product quality, operational reliability, and regulatory compliance.
Contact Micet’s team for a customized distillery equipment solution designed for your specific needs and production goals.
This guide was compiled using the latest industry data and expert insights from leading equipment manufacturers. For specific equipment recommendations, always consult with qualified professionals familiar with your local regulations and production requirements.