Industrial brewing equipment refers to the large-scale systems and machinery used to produce beer and other fermented beverages in commercial quantities. With the rising popularity of craft beers and microbreweries, there is increasing demand for advanced brewing technology to improve efficiency, quality, and output. This guide provides beer manufacturers everything they need to know about choosing and operating industrial-scale brewing hardware.
Overview of Industrial Brewing Systems
Industrial brewing equipment comes in various configurations from integrated to modular designs, catering to breweries with different production requirements. Key components include the brewhouse to convert starch into alcohol, fermentation and aging vessels, filtration systems, packaging lines, cleaning setups, etc. Modern industrial breweries leverage automation in production processes for precision control.
When selecting equipment, key factors to consider are:
Table 1: Key Considerations for Industrial Brewery Equipment Selection
Parameters | Details |
---|---|
Production Volume | Batch size, annual output capacity |
Product Variety | Number and styles of beers produced |
Physical Size | Floor space and site constraints |
Budget | Equipment costs and additional investments |
Process Customization | Flexibility for craft styles and experimentation |
Quality Control | Monitoring systems and automation capabilities |
Sustainability | Water, energy usage; cleaner production |
Staff Skill Level | Equipment operation and maintenance requirements |
Industrial Brewing Equipment Guide
Industrial brewing setups comprise complex interconnected systems catering to different functions in the beer production workflow.
Table 2: Major Types of Industrial Brewing Equipment
Equipment Category | Key Functions and Machinery |
---|---|
Milling | Hammer and roller mills to crush malt |
Mash Conversion | Mash filters, lauter tuns, mash kettles to extract sugars |
Wort Boiling | Copper kettles for boiling wort and hop additions |
Whirlpool | Vessels using centrifugal force to separate trub |
Cooling | Plate heat exchangers, wort chillers |
Fermentation | Open, closed tanks, conical fermenters with temperature control |
Maturation | Yeast separation, clarification, aging tanks |
Carbonation | Brite tanks, carbonation stones |
Filtration | Plate filters, centrifuges, separators |
Packaging | Canning lines, bottle fillers, kegging |
CIP Systems | Clean-in-place stations, cleaning chemicals |
Automation | PLCs, HMIs, sensors for data capture and control |
Modern commercial breweries utilize modular designs that allow customizing equipment to meet specific needs in terms of batch volumes, number of brands produced, packaging formats required, etc.
Capacities, Dimensions, Layouts
The production capacity, floor space, site plan and layout are critical aspects that influence equipment selection for industrial breweries.
Table 3: Equipment Capacities and Physical Parameters
Considerations | Details | Recommendations |
---|---|---|
Annual Volume | Dependent on target output | Select equipment scale aligned to capacity plan |
Batch Size | Linked to fermenter volumes | Standardize around key brands |
Vessel Numbers | Based on varieties produced | Keep minimal, optimize schedules |
Height Constraints | Clearances for tanks, pipes, platforms | Plan early for site conditions |
Floor Space | Adequate maintenance access | Minimize distances between modules |
Service Access | Utilities, waste removal | Ensure sufficient clearances |
Layout Flexibility | Expansion capabilities | modular designs assist future growth |
Thorough planning of production volumes, brand portfolio, batch sizes, and physical space availability is vital for determining equipment sizing and facility design. Expansion potential should be assessed during initial construction. Optimized layout focusing on workflow and servicing aspects reduces operating costs over the long term.
Suppliers and Pricing
There is a diverse range of brewery equipment suppliers catering to businesses of all scales. Buyers should evaluate vendors based on reputation, customization capabilities, and budget alignment.
Table 4: Brewery Equipment Suppliers and Indicative Pricing
Supplier Profile | Budget Estimates |
---|---|
Global conglomerates | > $5 million for turnkey mega-breweries |
Large stainless engineering cos | $2-5 million for integrated industrial systems |
Mid-sized manufacturers | $500k-2 million for modular breweries |
Custom fabricators | <$500k for nano and micro setups |
Pricing depends on factors like:
- Production capacity
- Degree of process automation
- Import duties and taxes
- Additional accessories and services
Requests for quotations with clearly specified requirements will get better responses from vendors. Site visits to existing installations is worthwhile.
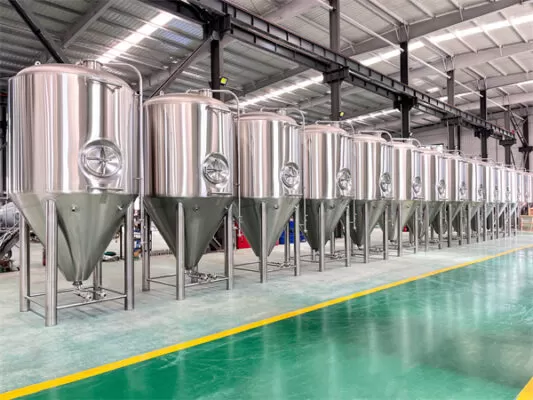
Installation, Operation, Maintenance
Meticulous installation, ease of operation, preventive maintenance, and prompt troubleshooting support are vital for industrial brewing hardware.
Table 5: Execution of Installation and Ongoing Equipment Management
Stage | Required Activities |
---|---|
Installation | Civil, structural, mechanical, electrical, piping works;<br> Equipment delivery handling; <br>Calibration, trial runs; |
Operation | SOP documentation;<br> Inspection schedules; <br>Water, energy, consumable supplies |
Maintenance | Preventive upkeep schedules; <br>Equipment monitoring; <br> Breakdown response planning |
Management | Training programs; <br>Spare parts inventory; <br>Suppliers feedback |
Brewers should validate construction readiness before equipment reach site. Staff training for standard operating procedures and maintenance tasks starts in the pre-commissioning phase. Energy, water, wastewater infrastructure should be ready before production rollout.
Selecting Brewery Equipment Suppliers
Choosing competent industrial brewing gear partners based on parameters like experience, scale, customization expertise, and post-installation support ensures smooth project execution.
Table 6: Vendor Evaluation Criteria for Brewing Hardware Procurement
Parameter | Assessment Criteria |
---|---|
Track Record | Years in business; Clientele size; Brewery portfolio |
Offerings Suitability | Equipment catalogs alignment; Budget fit |
Customization Skills | Design flexibility; Integration capabilities |
Order Fulfillment | Manufacturing reliability; Quality control |
Responsiveness | Quote turnaround times; Information transparency |
After-sales Service | Installation support; Maintenance contracts |
References | Client feedback; Brewery contacts for feedback |
Additional considerations for vendors include local presence, repair infrastructure, training services, spare parts supply assurance, and upgrades provisioning. Site visits to existing installations is advisable during selection.
Pros, Cons, and Limitations
Pros of Industrial Brewing Equipment
While the passion for a perfectly crafted beer might start small, scaling brewing operations demands equipment that can match ambition. This is where industrial brewing equipment steps in, offering breweries a world of advantages beyond simply increased volume. From consistent quality to operational efficiency, let’s dive into the key benefits that this equipment brings to the table.
Quality Ensured, Consistency Guaranteed: Imagine pouring the same beer twice and having vastly different experiences. Inconsistent quality can be the bane of any brewery’s reputation. Industrial equipment combats this by introducing precision and automation. Temperature control systems maintain optimal conditions for each brewing stage, minimizing human error and guaranteeing batch-to-batch consistency. Advanced filtration systems further elevate the game by ensuring clarity and removing unwanted particles, leading to a consistently smooth and satisfying final product.
Efficiency Reigns Supreme: Time is money, and industrial equipment understands this language perfectly. By automating tedious tasks like wort transfer and cleaning, it frees up valuable manpower for brewers to focus on their creative pursuits. Additionally, larger vessels allow for bigger batches, maximizing production output without compromising quality. This translates to increased profitability and the ability to meet growing demand with ease.
Scalability Made Simple: As a brewery grows, its equipment needs to grow with it. Industrial equipment is designed with modularity in mind, allowing breweries to seamlessly add new components or expand existing ones. This eliminates the need for costly equipment overhauls and ensures a smooth scaling process. Whether it’s adding a new fermenter or upgrading filtration systems, industrial equipment empowers breweries to adapt and thrive in a dynamic market.
Safety Always Comes First: Working with large volumes of hot liquids and pressurized systems demands a rigorous focus on safety. Industrial equipment incorporates robust safety features like pressure relief valves and automated shut-off mechanisms, minimizing the risk of accidents and ensuring a safe working environment for everyone involved.
Data-Driven Decisions: In today’s data-driven world, information is power. Industrial equipment often comes equipped with sophisticated monitoring systems that track temperatures, pressures, and other key metrics throughout the brewing process. This wealth of data allows brewers to gain valuable insights into their operations, identify areas for improvement, and optimize their recipes for even greater efficiency and quality control.
Sustainability in the Spotlight: As environmental awareness grows, breweries are increasingly focused on reducing their ecological footprint. Industrial equipment manufacturers are responding with innovative solutions that incorporate energy-efficient features and use sustainable materials. From heat recovery systems to water-saving cleaning protocols, these technologies allow breweries to brew their passion responsibly, minimizing their environmental impact.
Cons of Industrial Brewing Equipment
The allure of industrial brewing equipment is undeniable. It promises efficiency, precision, and the ability to scale production to new heights. Yet, for passionate brewers, the path paved with stainless steel behemoths might not always be smooth sailing. Before taking the plunge, it’s crucial to acknowledge the potential downsides of this powerful machinery.
The Price of Precision: While consistency is a virtue, excessive control can stifle creativity. Industrial equipment, with its automated routines and standardized processes, can leave little room for experimentation. The magic touch of a hands-on brewer, adjusting temperatures by feel or adding ingredients based on intuition, becomes less relevant. This homogenization might lead to beers that are technically flawless but lack the unique soul that craft breweries are known for.
Flexibility Forfeited: While modularity allows for growth, it doesn’t translate to instantaneous adaptation. Adding a new tank or changing a recipe within an industrial setup can be a complex and time-consuming process. Smaller brew systems, on the other hand, offer the agility to quickly tinker and adjust, embracing happy accidents and spontaneous recipe tweaks that can lead to exciting new discoveries.
The High Cost of Entry: The initial investment in industrial equipment is substantial. Not only are the machines themselves expensive, but their installation and maintenance require specialized expertise and infrastructure. This high barrier to entry can be daunting for small and aspiring breweries, potentially limiting the diversity of voices and brewing styles in the market.
Sustainability Skepticism: While strides are being made towards eco-friendly solutions, industrial equipment inherently consumes more resources than smaller setups. Large-scale brewing typically uses more water, energy, and cleaning chemicals, leaving a bigger environmental footprint. For breweries committed to sustainable practices, this trade-off demands careful consideration.
The Human Touch Fades: Automation is a double-edged sword. While it frees up manpower for other tasks, it also removes the brewer from the direct interaction with the ingredients. This detachment can lead to a disconnect with the brewing process, potentially dulling the passion and connection that draws many to the craft.
Limitations of Industrial Brewing Equipment
Industrial brewing equipment, with its imposing tanks and gleaming chrome, embodies the power of precision and scale. Yet, behind this façade of efficiency lies a world of limitations. Just as towering mountains offer breathtaking vistas but limit spontaneous exploration, these behemoths of brewing impose boundaries on the creative spirit, demanding a deeper understanding of their constraints.
Size Matters, But Not Always for the Better: While large batch sizes fuel profitability, they can also become creative handcuffs. Experimentation, the lifeblood of craft brewing, thrives on small-scale trials, allowing brewers to refine recipes and explore the subtle nuances of flavors. In contrast, large-scale brewing requires unwavering commitment to a recipe, leaving less room for spontaneous tweaks and serendipitous discoveries.
Flexibility Takes a Backseat: Unlike a sculptor with a lump of clay, brewers with industrial equipment navigate a predetermined path. Adapting recipes or incorporating last-minute ingredient changes becomes a logistical dance, requiring adjustments to temperature profiles and cleaning schedules. This rigidity can stifle the agility needed to seize fleeting opportunities and respond to dynamic market trends.
The Personal Touch Gets Lost: Stepping onto the platform of an industrial brewery, one might encounter a symphony of automated pumps and valves, but the human touch fades into the background. The intimate connection with the brewing process, the intuitive adjustments based on smell and texture, are largely replaced by data-driven decisions and pre-programmed cycles. This disconnect can impact the soul of the beer, potentially sacrificing the unique character and depth that defines craft brewing.
Standardization Breeds Similarity: From the gleaming tanks to the automated processes, industrial equipment embodies uniformity. While this consistency assures predictable outcomes, it can also lead to homogenization. The beers produced, while flawless in execution, might lack the distinctive personality and regional flair that excites craft beer enthusiasts.
Costly Upkeep, Environmental Footprint: The initial investment in industrial equipment is a hefty price tag, but the costs extend far beyond. Maintaining these complex systems demands skilled technicians and specialized cleaning protocols. Additionally, the sheer scale of operation translates to increased water and energy consumption, leaving a larger environmental footprint compared to smaller setups.
The limitations of industrial brewing equipment are not meant to dissuade, but rather to inform. Recognizing these constraints empowers brewers to make informed decisions, leveraging the strengths of these systems while seeking creative workarounds and embracing alternative approaches. Ultimately, the path to brewing excellence lies not in blindly adopting tools, but in understanding their limitations and using them to amplify, not constrain, the brewer’s artistry. Only then can the industrial giants dance in harmony with the creative human spirit, producing beers that celebrate both precision and soul.
Table 7: Comparison of Key Advantages Against Limitations
Parameters | Pros and Benefits | Cons and Challenges |
---|---|---|
Volumes | High outputs; Economies of scale | Coordination complexity; Inventory |
Automation | Precision; Repeatability; Data insights | Inflexible processes; Equipment costs |
Varieties | Capability to produce diverse brands | Additional tanks; Changeovers |
Quality | Advanced process control; Condition stability | Rigorous CIP needs |
Footprint | Compact compared to capacity | Site development needs |
Ops Skills | Specialized technical teams | Training overheads |
While modern industrial beer making equipment offers tremendous productivity and efficiency gains, brewers must weigh benefits against the significant capital and operating expenses involved.
FAQ
What are the typical costs for an industrial brewery equipment setup?
- Costs vary considerably based on production volumes and degree of automation – from around $500,000 for a basic 10,000 hl brewhouse to over $5 million for a 500,000 hl state of the art facility.
What are the floor space requirements for an industrial brewery?
- As a guideline, allow around 1.5-2 sq.ft. per annual barrel of beer produced for the brewhouse alone. More area is needed for fermentation, maturation, storage.
What are the most common beer making equipment brands?
- Leading global equipment OEMs include Alfa Laval, GEA Group, Krones, Paul Mueller and Praj. Many custom stainless steel fabricators also cater to industrial breweries.
What production volumes define a micro vs macro industrial brewery?
- Microbreweries produce less than 15,000 barrels per years. Large macro breweries output over 6 million barrels annually.
How much time does an industrial brewery installation require?
- Timelines span 6-12 months based on scale – covering site preparations, equipment delivery schedules and installation, trial runs, test brewing, commercial launch.
Just wish to say your article is as surprising The clearness in your post is just cool and i could assume youre an expert on this subject Fine with your permission allow me to grab your RSS feed to keep updated with forthcoming post Thanks a million and please keep up the enjoyable work